
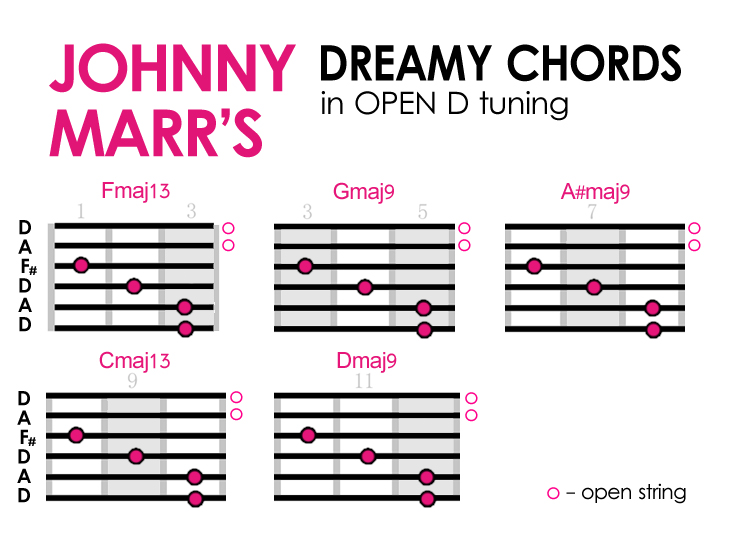
The response to a step set point change and a step load change for a self-regulating process response with lambda tuning is shown in figure 2.įigure 2. Though lambda is defined as the closed loop time constant of the process response to a step change of the controller set point, the load regulation capability is also a function of the lambda of the loop. Lambda tuning for self-regulating processes can result in a closed loop response that is slower or faster than the open loop response time of the process. More importantly, the lambda of the loop can be used to coordinate the responses of many loops to reduce interaction and variability.

This could result in choosing a small lambda for good load regulation, a large lambda to minimize changes in the controller output and manipulated variable by allowing the PV to deviate from the set point, or somewhere in between these two extremes. The lambda closed loop response time is chosen to achieve the desired process goals and stability criteria. The lambda tuning method allows the user to choose the closed loop response time, called lambda, and calculate the corresponding tuning. Tuning for a self-regulating processĪ tuning methodology called lambda tuning addresses these challenges. The desired aggressiveness of the loop tuning should be based on the interaction of the control loop with other loops and the consequences of movement of the controller output. Finally, the interaction of the control loop to be tuned with other control loops should be reviewed and understood. Also, the control scheme should be reviewed to make sure it is an appropriate, linear, control scheme for the application. ANSI/ISA-75.25 and the EnTech Control Valve Dynamic Specification V3.0 are excellent sources of information on this topic. It should have a response time that is appropriate for the process performance requirements. The control valve should have a small deadband and resolution - another topic of discussion! It should have an appropriate and consistent flow gain. Before tuning a controller, it is helpful to have an understanding of the process and to verify the performance of the instrumentation and final control element, usually a control valve. Regardless of the tuning of the PID controller, the control performance is limited by the performance of the instrumentation and final control element. In this article, I will present a method to tune PID controllers on self-regulating processes. In the March/April issue of InTech, I presented techniques for tuning a PID controller used on an integrating process. Many flows, liquid pressures, temperatures, and composition processes are self-regulating. Self-regulating responses are very common in the process industry.
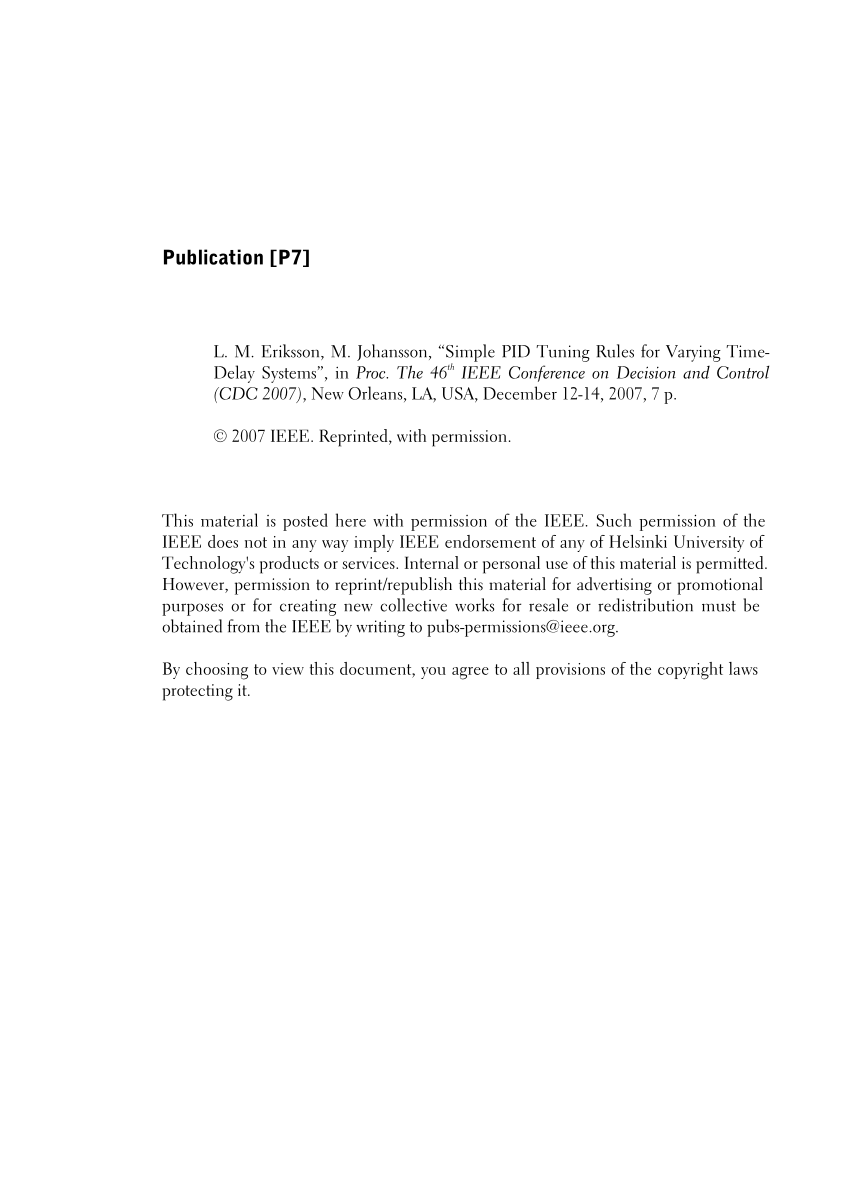
Response of the PV to a step change of the controller output for a self-regulating and an integrating process Figure 1 compares the response of the process variable to a step change of the PID controller output for a self-regulating process and for an integrating response.įigure 1. The output of the process, the process variable (PV), is the input to the PID controller. From the standpoint of a proportional, integral, derivative (PID) process controller, the output of the PID controller is an input to the process. An integrating process response to a step input change is characterized by a change in the slope of the process variable. A self-regulating process response to a step input change is characterized by a change of the process variable, which moves to and stabilizes (or self-regulates) at a new value. The two most common categories of process responses in industrial manufacturing processes are self-regulating and integrating.
